FabLab turns 10 On the cutting edge of high-tech manufacturing, North Forge Fabrication Lab still has homemade vibe
Read this article for free:
or
Already have an account? Log in here »
To continue reading, please subscribe:
Monthly Digital Subscription
$1 per week for 24 weeks*
- Enjoy unlimited reading on winnipegfreepress.com
- Read the E-Edition, our digital replica newspaper
- Access News Break, our award-winning app
- Play interactive puzzles
*Billed as $4 plus GST every four weeks. Offer only available to new and qualified returning subscribers. Cancel any time.
Read unlimited articles for free today:
or
Already have an account? Log in here »
Hey there, time traveller!
This article was published 27/10/2021 (1224 days ago), so information in it may no longer be current.
The North Forge Fabrication Lab (it was originally called AssentWorks) was entirely built by volunteers who put up the drywall and insulation and scrounged tools and equipment from sympathetic companies like Princess Auto, who are still sponsors today.
On the occasion of its 10th birthday party on Wednesday, the place which effectively formed the foundation of Winnipeg’s startup ecosystem, still has that homemade feel about it. (Prince Charles trundled up the three flights of grungy stairs during a visit in 2014.) But it now houses more than $3 million worth of sophisticated equipment like CNC machines, laser cutters and 10 3D printers as well as a new forming machine that Joelle Foster, CEO of North Forge, said was the very piece of equipment George Lucas used to make the original white armour for Star Wars’ stormtroopers.
That same piece of equipment was used by recent FabLab member, Rob Ranson, to quickly produce a prototype for a one-piece COVID face shield that covers the whole head.
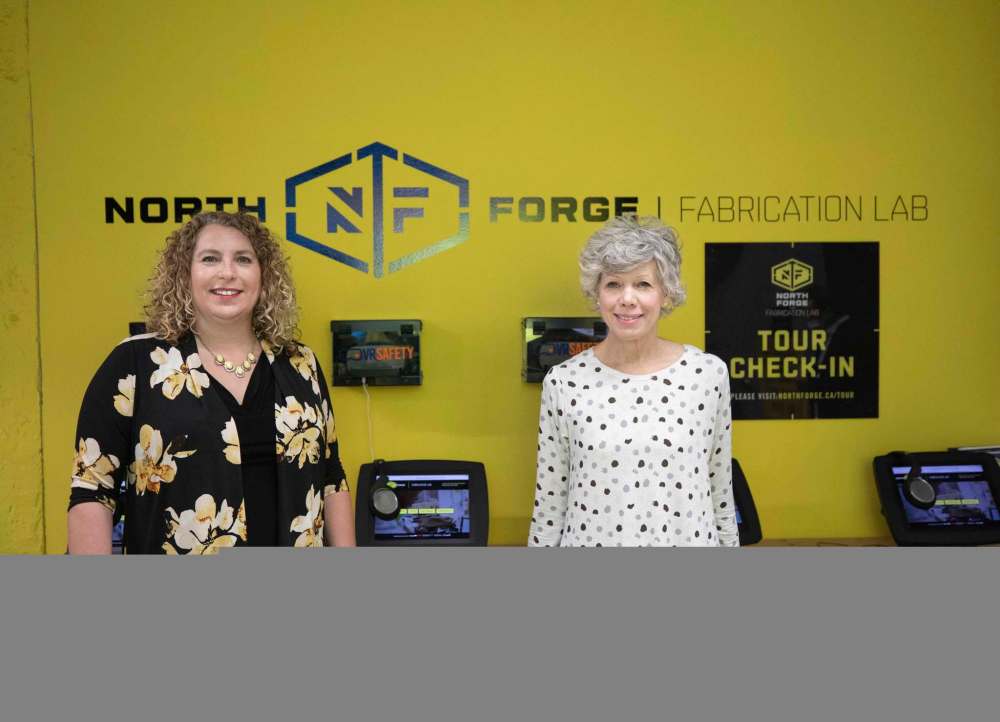
At the start of the pandemic Ranson was the managing director of the department of otolaryngology at Health Sciences Centre. He had grave concerns that the personal protective equipment his staff and doctors had at their disposal did not provide sufficient coverage.
He was so frustrated he woke up one morning at 3 a.m. and sketched out a design.
He knew about the North Forge Fabrication Lab and called Marney Stapley, the general manager of the lab, and she contacted three FabLab members with experience in design, use of CNC cutting equipment and Matt Olson, a serial entrepreneur and the FabLab’s longtime manufacturing mentor.
“Three days later we had a prototype built,” Ranson said.
About a month later he had a contract from HSC and nine months later he delivered the product. There are now millions of the shields in use.
“Rob is an incredible inventor,” Foster said.
He’s now in the process of developing a number of other medical devices and his new company, Win-Shield Medical Devices Inc., has graduated to the North Forge incubation program.
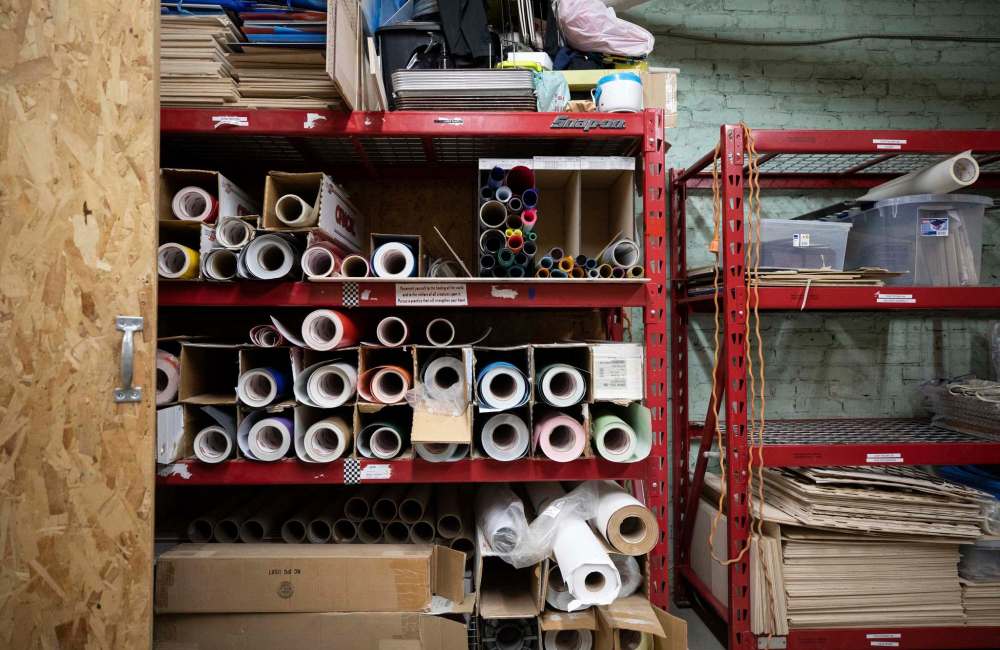
Ranson is the latest poster child for what the FabLab is all about.
It is the largest publicly accessible fabrication lab in North America. Members pay $155 per month for 24-7 access to the 15,000-square-foot facility which grew by 6,000 square feet at the beginning of the pandemic when space on the first floor of the old Swift Canadian Wholesale Market building in the West Exchange became available.
“We have let the landlord know that as more space comes available we would love to eventually have the whole building,” said Foster.
Although there are only about 100 active members right now, over the years more than 2,300 entrepreneurs, tinkerers, and business founders have used the space.
It has now become a Safe Work-certified space. New members have to undergo a significant training program which includes a virtual reality component designed by North Forge graduate company Bit Space Development Ltd.
With about two and a half full-time staff, Stapley said it is still largely run by volunteers.
“It used to be a bit “wild west” here,” she said referring to the lax rules of the past.
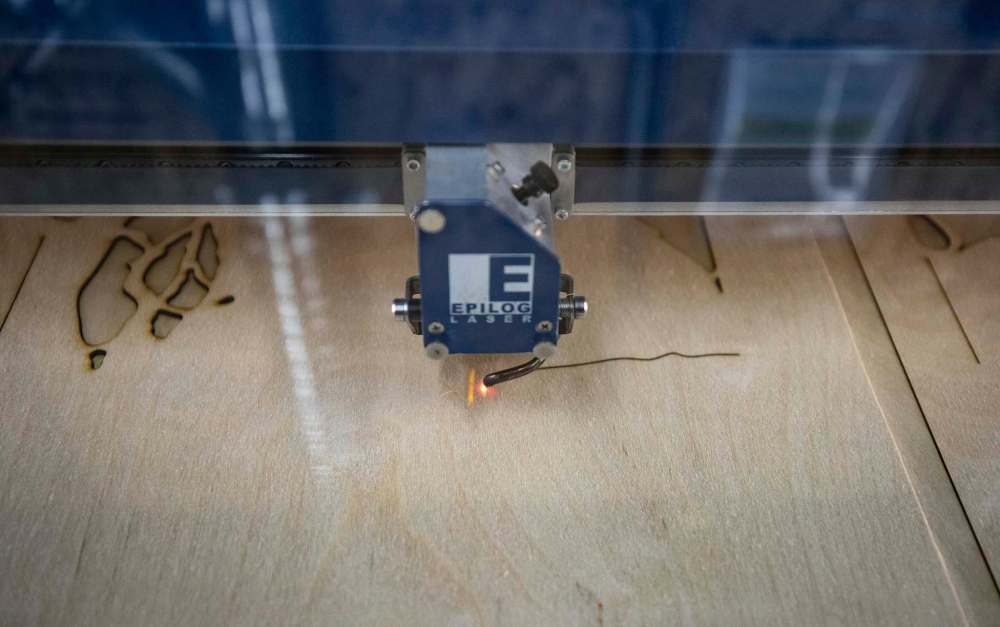
Originally built by four Winnipeg entrepreneurs — Michael Legary, David Bernhardt, Chris Johnson and Kerry Stevenson — it effectively formed the foundation of the startup ecosystem that has ensued.
Legary, a longtime Winnipeg cyber-guru, Johnson, the founder and CEO of Permission Click, and Stevenson, the founder of the largest 3D-printing blog in the world called Fabbaloo, can all still be found at the FabLab on any given Tuesday night when it holds regular open houses. Bernhardt flew in from Vancouver for the 10th anniversary.
Before the party began on Wednesday afternoon, Graeson Fehr was busy in his small metal shop on the first floor, where he makes homemade hunting and fishing knives for his company Fehr Forgeworks.
Dennis Bergen was in the process of cutting out birch-wood Christmas decorations on a new $100,000 laser cutter that had to be purchased recently because the other three were kept so busy by about 25 entrepreneurs who were using them night and day. Bergen, who owns a company with his wife called Zealous Décor, was finishing up an order for hundreds of decorations for Pine Ridge Hollow.
Ava Foster, (no relation to Joelle) who is on the FabLab’s member council, is an artist who makes wood carvings. She works with woodworking machines and hand carves her pieces.
“Without the FabLab I would not be able to access the machines I need to make what I do, so it’s crucial for me,” she said.
The FabLab has enjoyed support from the community. Princess Auto provides enough gift cards for Stapley and her team to replenish their tools whenever they need to. Bockstael Construction backs a dump truck into the laneway every two weeks to haul away the garbage. Companies including Bell MTS and PCL Construction have provided ongoing support over the years and all of them provide annual cash and in-kind support.
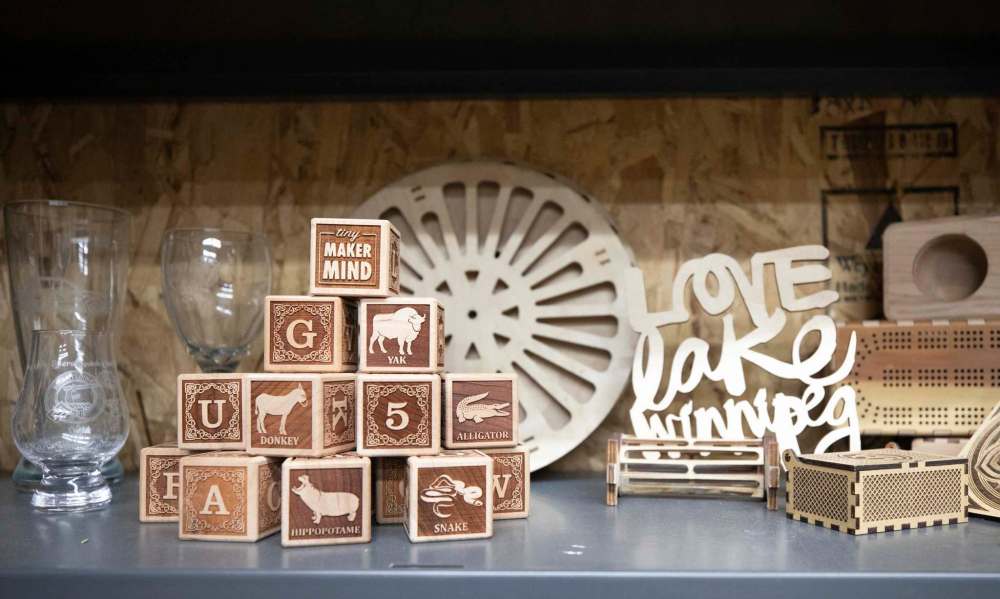
Over the years the FabLab has become the meeting place for everyone from established companies like Barkman Concrete, which does much of its new product prototyping, and all sorts of other dreamers.
“It’s a community of eclectic people here,” said Ava Foster.
martin.cash@freepress.mb.ca
Awards of recognition
Customized maps of Innovation Alley by Randy Merrit of Silver Birch Design — were given out to:
Doug Campbell — the Current Builder Award. Campbell is the member council chair, a member of the Green Team, the Bockstael Carpentry Room lead trainer, Health and member of the safety committee and VRSafety program.
Avery Anne — Excellence in Community Culture. Anne is the member council vice-chair, a member of the Green Team, on the Health and Safety Committee and provides leadership and guidance to all members.
Robert Elms — Long Standing Volunteer. Elms is the community outreach lead and conducted tour groups for the last 10 years resulting in over 2,000 volunteer hours.
Matt Olson — Long Standing Member and Mentor. AssentWorks was built for people like Matt who wanted to build a snowboard company and he did — Home Snowboards. Matt has built several other businesses out of the FabLab over the last 10 years. He currently is the founder of Prysm Manufacturing and the manufacturing mentor at the FabLab.

Martin Cash
Reporter
Martin Cash has been writing a column and business news at the Free Press since 1989. Over those years he’s written through a number of business cycles and the rise and fall (and rise) in fortunes of many local businesses.
Our newsroom depends on a growing audience of readers to power our journalism. If you are not a paid reader, please consider becoming a subscriber.
Our newsroom depends on its audience of readers to power our journalism. Thank you for your support.